I wasn't sure whether to post this in implements or maintenance and repair.
A couple of weeks ago I bought a WW Grinder Super Apache chipper/grinder/shredder to use with my Kubota B8200HSD. It was used very little but allowed to sit in the elements. WW Grinder is long out of business, the chipper was probably made in the 80s.
The PTO shaft is frozen so that it won't telescope. I know there are lots of threads on how to try to separate the two halves, but they mostly start with the plastic shield removed.
With some effort I was able to get the implement end of the shaft removed from the chipper. It has an integrated shear bolt assembly on that end making it an unusual shaft.
I'd like to at least like to be able to release the bell shaped guard on the end of the shaft and slide it towards the middle so I can see the yoke and what is going on there.
The guard says G&G on the side.
Below I'll show a photo of the shaft. The second little picture shows the type of spring clip that seems to be use in the shaft. Do I just pull on it to slide the clip a bit to be out of the way? The third picture shows the through hole. The silver nuts and bolts were my make-do screw jack to push the PTO shaft off of the implement shaft stub.
I'm also curious what a replacement shaft would cost. The implement end has facing flanges that take a 1/4-20 shear bolt between them but still are connected against axial pull with the bolt out.
The male shaft stub on the implement measures about 1.18" OD with 1/4" keyway and a 5/16? through hole.
So I assume the pto shaft is smooth bore female 1-1/4" ID with 1/4" keyway and a 5/16 through hole.
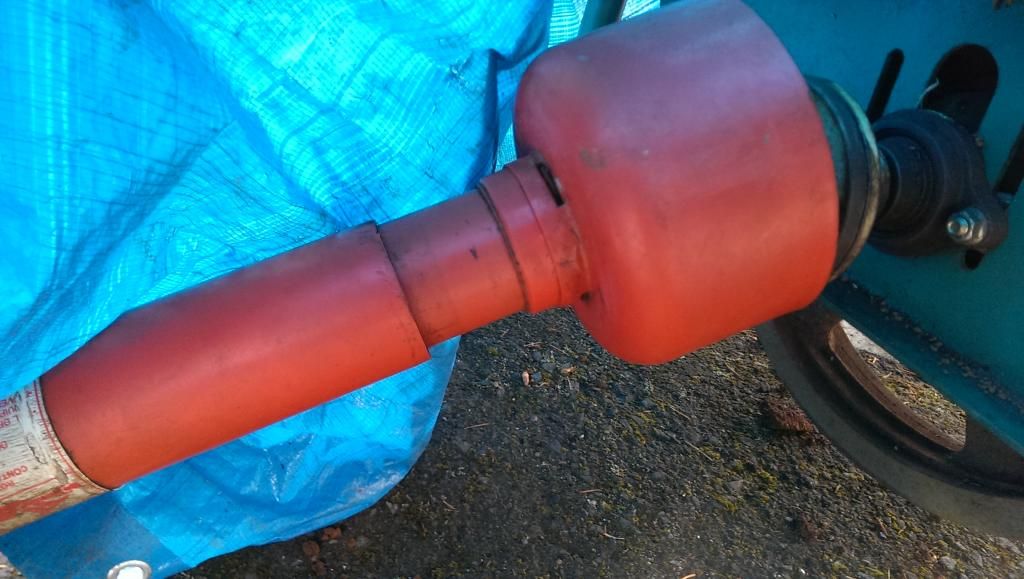
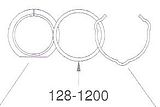
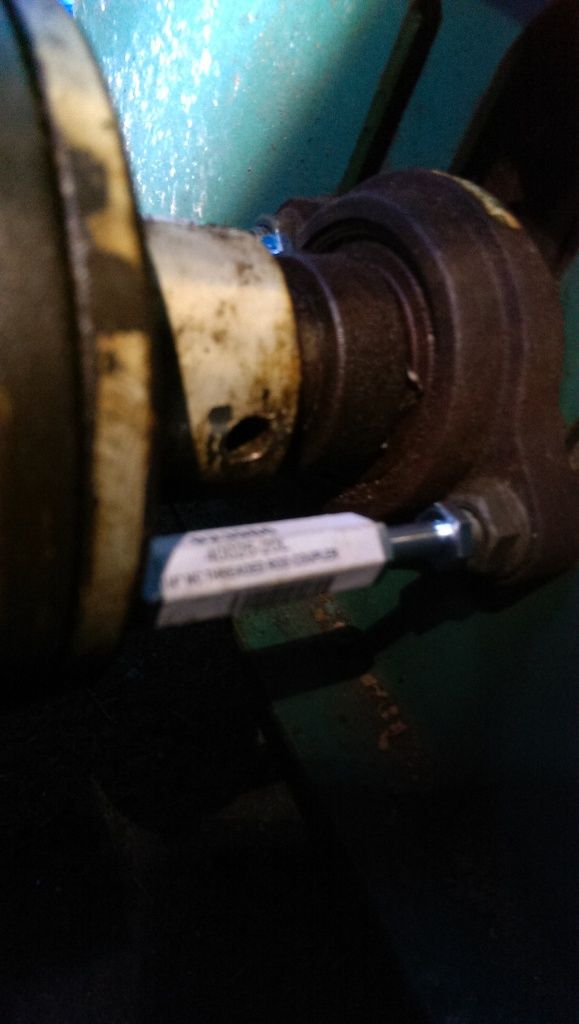
A couple of weeks ago I bought a WW Grinder Super Apache chipper/grinder/shredder to use with my Kubota B8200HSD. It was used very little but allowed to sit in the elements. WW Grinder is long out of business, the chipper was probably made in the 80s.
The PTO shaft is frozen so that it won't telescope. I know there are lots of threads on how to try to separate the two halves, but they mostly start with the plastic shield removed.
With some effort I was able to get the implement end of the shaft removed from the chipper. It has an integrated shear bolt assembly on that end making it an unusual shaft.
I'd like to at least like to be able to release the bell shaped guard on the end of the shaft and slide it towards the middle so I can see the yoke and what is going on there.
The guard says G&G on the side.
Below I'll show a photo of the shaft. The second little picture shows the type of spring clip that seems to be use in the shaft. Do I just pull on it to slide the clip a bit to be out of the way? The third picture shows the through hole. The silver nuts and bolts were my make-do screw jack to push the PTO shaft off of the implement shaft stub.
I'm also curious what a replacement shaft would cost. The implement end has facing flanges that take a 1/4-20 shear bolt between them but still are connected against axial pull with the bolt out.
The male shaft stub on the implement measures about 1.18" OD with 1/4" keyway and a 5/16? through hole.
So I assume the pto shaft is smooth bore female 1-1/4" ID with 1/4" keyway and a 5/16 through hole.
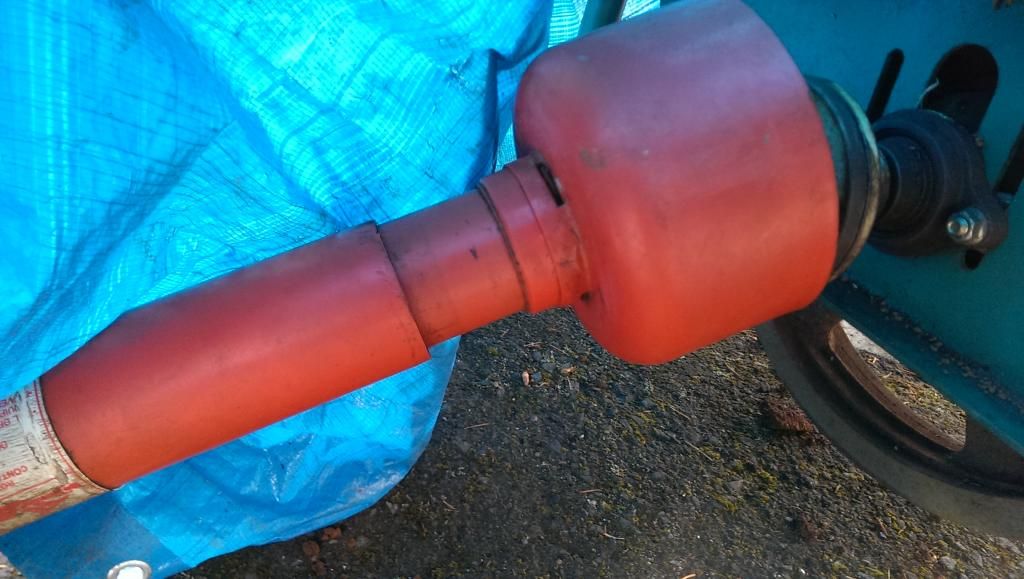
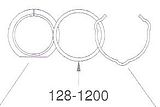
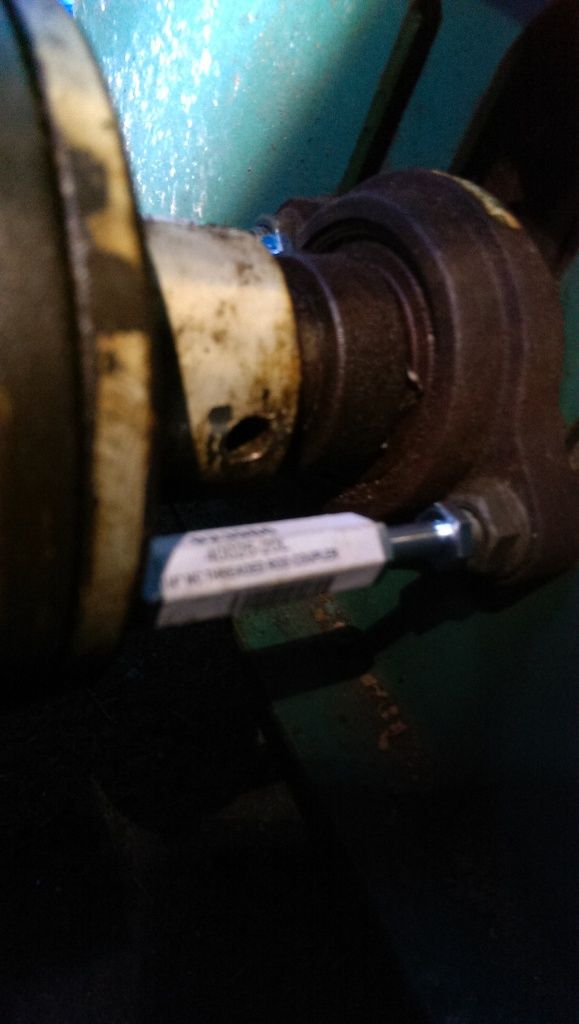